The Internet of Things is a complete concept that includes not only remote sensor data acquisition, transmission, storage, and display, but also analysis of collected sensor historical data, as well as decision-making, feedback, and control actions based on the results of the analysis. Compared with traditional human cognition, the Internet of Things is equivalent to enhancing the recognition ability of people's "five features", enabling people to obtain information that is not directly available. The data analysis based on the Internet of Things is equivalent to enhancing the perception of the human brain, enabling people to get rid of the limitations of traditional thinking and achieve more dimensions, more comprehensive, and more real-time cognitive and judgment skills.
Big data in the usual sense refers to the calculation of bulk data. Due to the limited storage and computing power, a series of new technologies including Hadoop and Spark have been developed in the past decade to process massive amounts of data (mainly bulk data) in an efficient and real-time manner. The original data mining technology that deals with small data sets is combined with big data to realize analysis of many business system data (bulk data-based), such as classification and portraits of different label groups, and precise marketing. . With real-time improvements, streaming computing and analysis have been mentioned in recent years at a higher level to process time-tagged data, such as IoT data, that needs to be analyzed and processed at all times. Log data.
As you can see, these two seemingly unrelated technologies can be tied together by data (a data generation, a processing and analysis data).
IoT, IIoT and industrial big data need to be traced back to the source
Before I elaborate, I need to help you distinguish between several concepts.
First distinguish between traditional Internet of Things and Industrial Internet of Things
Traditional Internet of Things (IoT) focuses on consumers and smart cities. By adding a large number of widely distributed sensors to collect and transmit real-time data, it can build real-time monitoring, display, alarm and historical data query capabilities. Industrial IoT mainly refers to Collect control system data of existing industrial equipment (rarely need to increase sensors), and based on monitoring alarms, through in-depth data analysis, find ways to improve equipment reliability, reduce anomalies, and improve production and operational efficiency.
The traditional Internet of Things data analysis, and our flow data analysis on the Internet, is not much different. Through the processing of a single indicator, the average and extreme values ​​in the corresponding time window are generated, and batch calculation and display are performed.
Differentiating Industrial Internet of Things and Industrial Big Data
In many foreign manufacturers and media, there is no concept of industrial big data, more is to merge it into the category of industrial Internet of Things (IIoT), while the domestic regards the two as two different categories, and at the same time, Together with technologies such as production and supply chain systems, they are integrated into the concept of the industrial Internet. Therefore, we can see that foreign analysis institutions, including Gartner, do not specifically classify industrial big data or industrial Internet, but have a very detailed analysis of IIoT.
In the traditional industry, there is no data processing. However, the original data collection, data processing, data analysis and feedback are scattered in different systems. On the one hand, it is unable to deal with a large amount of industrial "big" data, on the other hand, it cannot guarantee real-time. We often see industrial companies, many data analysts are forced to manually export some data files from different control systems, cross-correlation and labeling by hand, and write the corresponding Matlab program to achieve statistical analysis and modeling, and then Extract some field data for verification, and companies with good conditions will also invite some external partners to develop them into applications. The efficiency of such processing and analysis is really low, but it is indeed a common phenomenon.
Industrial Internet of Things and Internet big data analysis are very different
The data analysis of industrial Internet of Things (Industrial Internet of Things + Industrial Big Data) has many differentities from traditional Internet big data analysis.
1, the data attributes are different
Huge amount of data
The "quantity" of industrial data needs to be considered in several ways:
More data dimensions
The traditional Internet of Things, because it is usually relatively independent sensors, and the data points on each sensor are often single digits, so the data dimension is very small.
For industrial IoT, complex production is a process in which multiple processes are interrelated and each process is multidimensional data integration.
The data dimensions mentioned here cover various equipment characteristics, external working conditions, parameters, materials and process recipes in the production process. This dimension is often in the order of thousands. In many high-end automated productions (such as semiconductors), the data dimensions reach tens of millions of levels, and any one of the variables in any of these processes may change. The result of the final production produces a butterfly effect.
Diversified sampling frequency
The data collection interval of the traditional Internet of Things is usually in the order of seconds and minutes, which is relatively fixed.
The sampling frequency of industrial equipment data is very large, and the different indicators of one device can be thousands of times different. For current and vibration acceleration sensor indicators commonly used in equipment fault diagnosis, sampling frequencies above 10KHz are often required, and some state changes often take only a few seconds or even tens of seconds to sample.
Large data time span
Long-term data retention is very helpful for characterizing the accumulation of features in different states. The traditional IoT needs to preserve long-term data is not very obvious, there is not much demand for "Stateless". But the Industrial Internet of Things, for stateful data analysis, is very demanding.
First of all, in the traditional industrial field, the setting of equipment status, control thresholds and key parameters is often set and adjusted by the experience value of the manufacturer or operator. Whether this value is correct or not requires long-term data verification. ;
Secondly, the current, power, torque and other indicators of industrial equipment often have distinct characteristics under different working modes, working conditions and fault conditions. These features, if saved, can be used to train the feature recognition model through machine learning, which will help to achieve accurate state judgment, anomaly detection and fault diagnosis. Also, by continuously accumulating data samples similar to the same tag, it will help to enhance the accuracy of the recognition. In particular, some highly reliable critical equipment, because the cost of failure is high, it is necessary to save the characteristics of abnormal or fault, and further improve the reliability through the combination analysis between components, subsystems and features between devices. Sex.
2, real-time strong
It is generally believed that the real-time nature of industrial data can be strong, but this often refers to the real-time nature of industrial control, rather than the real-time nature of industrial data analysis.
Traditional industrial data analysis often involves intercepting a piece of data in a control system or software system, saving it into a file, writing a piece of code (such as Matlab) and a model through an analyst, testing and verifying it in an experimental environment, and then developing the corresponding The control logic or application evaluates the developed model through real-time reception and continuously adjusts the parameters of the model during the run. This process is very painful, not only because the source of the data and the analysis are out of line, but also because the real-time data validation in the process of model development is not possible in the existing environment.
The ideal industrial data analysis should be an efficient and real-time process. It can extract valid data samples from real-time industrial data, develop specific algorithms and models based on different development languages ​​and model frameworks, and validate based on real-time collected data, and then compare the verification results with real real-time data streams. Combined, real-time judgment is achieved. Only in this way can intelligent analysis and control for specific scenarios be formed.
3, poor data quality
Poor industrial data quality is a typical feature of industrial data.
The professional nature of the industry has led to the large integration of large equipment from subsystems from many different manufacturers. The OEM often does not understand the working principle of each subsystem, and does not form a complete, cross-subsystem control logic and data integration mechanism. Therefore, only some key control signals can be selected from them to achieve the established control logic. Instead of caring about how each subsystem works, it includes a variety of non-control metrics that contribute to reliability, efficiency, and even quality analysis.
On the one hand, although industrial equipment manufacturers all claim to be able to achieve various indicators, they often only guarantee the integrity of key control indicators, but can not guarantee the accuracy and reliability of key subsystem indicators;
On the other hand, because there is no good data integration mechanism, it is often impossible to identify the working status of different subsystems, and it will cause huge obstacles to the later analysis of data for different working states;
Third, integration from different subsystems often leads to common errors such as time label inconsistency, incorrect data range, and incorrect data labeling. Even in the event of a problem, the OEM cannot explain the meaning of the subsystem.
At the same time, due to the harsh conditions of the on-site environment, sensor data is often invalidated or inaccurate for a long time;
These data quality problems have caused huge obstacles to the later data analysis, and a lot of cleaning and processing work needs to be done before the analysis.
Different data analysis methods
When it comes to big data analysis, many people naturally think of clustering, classification, and mining of massive data to achieve accurate marketing and user portraits.
However, the data of these Internet or business systems have some significant assumptions, that is, the amount of data is large, the data can be clearly labeled, the standardization scenarios are many, and the accuracy of the analysis is not high. Through a series of classification and mining, common features between different samples can be found, and the characteristics of individuals with the same or similar attributes can be inferred for the training results of different individuals with similar attributes.
Industrial Data Analysis Challenge
Â
However, in industrial data analysis, these assumptions are basically non-existent, and data analysis faces more challenges:
Small sample
Industrial anomalies tend to be very small, or the probability of occurrence on a single device is very low, which makes it impossible to use conventional big data, machine learning methods, to train a stable fault model based on the acquired abnormal data characteristics;
Overfitting
According to a large number of relevant factors, the model trained by machine learning under a specific data set, even after a large amount of test data verification, shows a perfect fitting feature, but in the real environment, due to the data and working state It is often difficult to obtain long-term stable judgment results, that is, the situation of “over-fitting†occurs.
Difficult to accurately and clearly mark
Industrial data, even if there are some features that can be refined, but this feature is often closely related to different working conditions or working modes (such as the vibration amplitude of the vibration sensor, completely different under light load or heavy load) If there is no way to distinguish the labeling conditions of abnormal features, it is difficult to achieve effective data filtering and analysis;
Scene fragmentation
Industrial scenes are very fragmented, and it is difficult to have a common model, even if there are some fault models like motors and pumps, as well as general analysis methods such as vibration analysis and SPC, on different types of equipment, even in different types of individuals. On the top, it is difficult to guarantee a uniform and stable operation.
These challenges will lead to industrial big data analysis. It is impossible to fully adopt the analysis method of Internet big data, but it is necessary to fully combine the working mechanism to achieve compound modeling and judgment.
Industrial data analysis classification
In general, data analysis of industrial Internet of Things can be divided into the following four categories:
Descriptive analysis: Statistics and display of collected IoT data, which is mainly based on statistical analysis;
Diagnostic analysis: Combining industrial mechanisms to diagnose and analyze the causes of abnormalities, this part needs to add a lot of data mining techniques, including correlation analysis, sequence event analysis, etc.
Predictive analysis: predicting changes in trends through the development of long-term historical data. This part needs to introduce technologies such as machine learning and neural networks to predict trends;
Prescriptive: Through the results of data analysis in multiple dimensions, combined with knowledge base and machine learning, it gives the possibility of multiple decision-making and provides intelligent judgment support.
In each category, analysis must be carried out from two levels:
Mechanism analysis: According to the principle of physics or chemistry, the professional control based on the design principle is carried out on the control, process and response of industrial equipment. This part must be based on professional knowledge;
Data-driven analysis: For many phenomena in the industry that cannot be measured and cannot be explained, you can extract the data features, find abnormal points from the massive data, and make up for the lack of professional knowledge through machine learning methods.
It can be seen that the basis of industrial data analysis is the industrial mechanism, that is, the understanding of professional industrial knowledge, rather than the methods and capabilities of data analysis. Without sufficient industrial mechanism and expertise, blindly analyzing some industrial data with big data and artificial intelligence tools will definitely be counterproductive.
The application scenario is integrated into the three major layers of industry and plays a huge role.
We all know that the application scenarios of Internet big data include accurate marketing based on user portraits and massive structured decision support. What kind of scenarios can the data analysis of the Industrial Internet of Things be applied to?
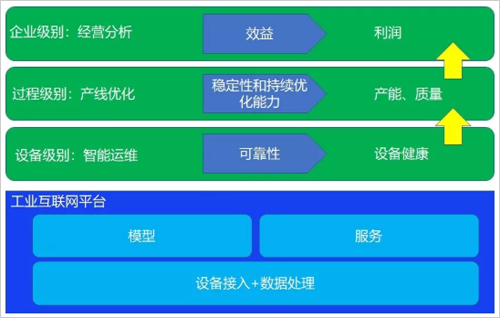
We believe that the big data analysis of the industrial Internet of Things can play a huge role from the three levels of industry.
1, the device layer
Industrial enterprises can construct visual remote monitoring by reading various real-time parameters of sensors or control systems of intelligent industrial products, and provide historical data collected, and build hierarchical indicators of components, subsystems and even the entire equipment. Use artificial intelligence to achieve trend forecasting; based on forecasted results, optimize maintenance strategies and spare parts management strategies to reduce and avoid customer losses due to unplanned downtime;
For example, the company provides a predictive maintenance and fault-assisted diagnostic system for drilling equipment for a petroleum machinery manufacturing company. It not only collects the key subsystems of the rig in real time, such as generators, mud pumps, winches, and top drives. The indicator data is more able to evaluate the performance of key components based on the development trend of historical data, and adjust and optimize the maintenance strategy according to the results of component performance prediction. At the same time, according to the analysis of the real-time status of the drilling rig, the drilling Efficient evaluation and optimization can effectively improve the input-output ratio of drilling.
2, the process layer
Industrial enterprises can integrate various elements of the production stage, such as raw materials, equipment, process recipes and process requirements, into a closely coordinated production process through digital means, and automatically complete under different conditions according to established rules. The operation realizes the automated production process; at the same time records various types of data in the production process, providing a basis for subsequent analysis and optimization.
Through the collection of real-time operational data of various production equipment on the production line, the visual monitoring of all production processes can be realized, and the monitoring parameters of key equipment parameters and inspection indicators can be established through experience or machine learning, and the abnormal situation with violation of the strategy can be processed in time. Adjustments to achieve a stable and continuously optimized production process.
For example, the online quality monitoring system built by Yunyun Technology for an electronic glass production line fully collects the data generated by the cold end and hot end equipment, and obtains the most ideal specifications of the key indicators in the process of production through machine learning. The SPC monitors the alarm strategy and analyzes the specific quality anomalies in tens of thousands of data collection points through correlation analysis.
3. Management layer
Industrial enterprises can build a unified data standard by combining various OT data generated by the process layer with various types of IT data generated or reported by the business system, and on the basis of this, through certain calculations and analysis, it can be generated. Accurate management level analysis provides support for the company's safe production, operational efficiency, decision support, and gradually extended to the external environment of the enterprise, providing an open data ecosystem, and thus forming a stronger competitiveness.
For example, Send Cloud Technology provides a provincial energy group with a solution for safe production control, extracts real-time data from dozens of different types of real-time databases, and combines business data extracted from third-party business systems to build multiple dimensions. The unified data standard, based on IT and OT integration data standards, develops a series of industrial applications including production operation monitoring, safety management, environmental management, quality management, energy management, business analysis and so on.
Having said that, many people can't help but ask, there is not a lot of data analysis, including BI and big screen display, there are many analysis reports, why should we increase the data analysis based on industrial Internet of Things?
We all know that the current industry data analysis, including the above display and report, is based on the business system, many of which are filled in data, or based on the calculations generated by the reported data. The data of the control system and the corresponding analysis results are free from the existing data analysis system. However, the actual reflection of the equipment, production and operation of the enterprise, if there is no data from the control system and the corresponding analysis, is seriously distorted. At the same time, many OT analysis, if there is no correlation from the IT system, can not get accurate results (such as the combination of maintenance records and production data to achieve quality analysis).
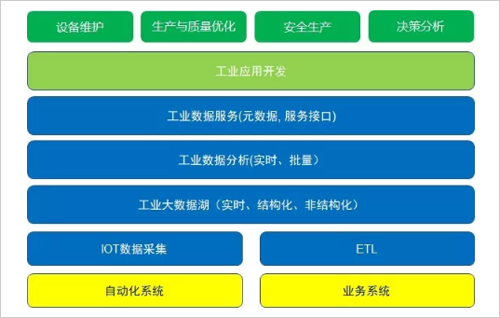
Schematic diagram of industrial IT/OT data fusion platform architecture
An efficient industrial enterprise, according to our understanding, must integrate OT and IT data into a large platform and develop strict data standards (assets, processes, processes, organizational standards) through different professions. Data analysis and continuous development of different new forms of application (as shown in the above figure) can meet the needs of the company's comprehensive, accurate and efficient operation. (The next one will discuss the integration architecture of IT and OT for industrial enterprises, and preview in advance)
Enterprises choose the industrial IoT platform will win the future
To sum up, the Internet of Things, whether it is the general Internet of Things or the Industrial Internet of Things, can not support the future development strategy of the enterprise without a combination of professional and refined data analysis. Choosing the right industrial IoT platform will greatly accelerate the digitalization process of the enterprise and advance rapidly toward the intelligent road.
Sending Cloud Technology is the leader of domestic industrial Internet of Things. It provides data acquisition, data cleaning and pre-processing, massive data storage and query for PLC, DCS, CNC and other equipment and business systems. It can effectively realize OT data. Efficient integration with IT data and providing unified data standards and data services. At the same time, it supports users to self-select data according to industrial mechanism, quickly build various industrial models, provide users with various visual development tools, quickly analyze and display data in real-time and business systems, and provide a series of application frameworks to support users. By configuring and zero-code or low-code, building predictive maintenance of equipment, visualization and quality optimization of production lines, and business analysis of the enterprise, helping companies build data-centric transformation strategies that eliminate the gap between different systems. Separate, fast, flexible and efficient insight into various problems in production and operation, and build sustainable competitiveness.
Tamping Rammer is perfectly balanced to
deliver hard hitting compaction as well operator comfort delivering low noise
and vibration to the operator.
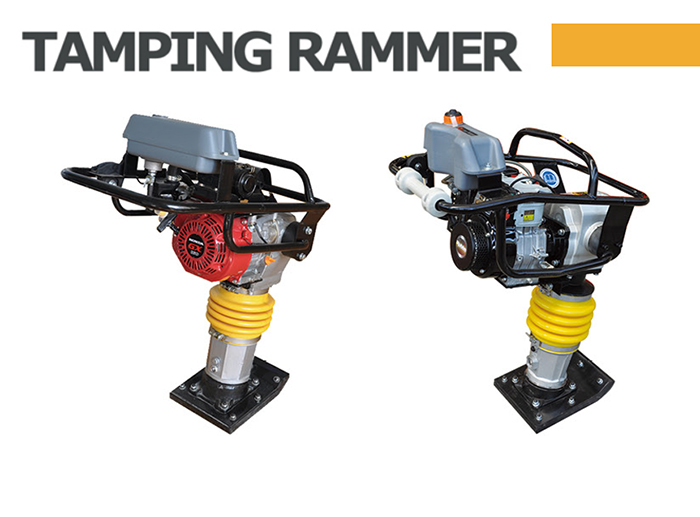
Tamping Rammer Features:
-Reliable four stoke engine delivers low
emission and noise;
-Ingenious throttle lever for smooth
operation;
-Heavy shock mount system reduces hand-arm
vibration and improves operator comfort;
-Durable plastic oil tank offers longer
life and rust-free;
-Laminated wood and steel shoe absorbs and
withstands vibration shock;
-Protective top frame cover eliminates possible
damage to the engine.